IPCL manufacturing process
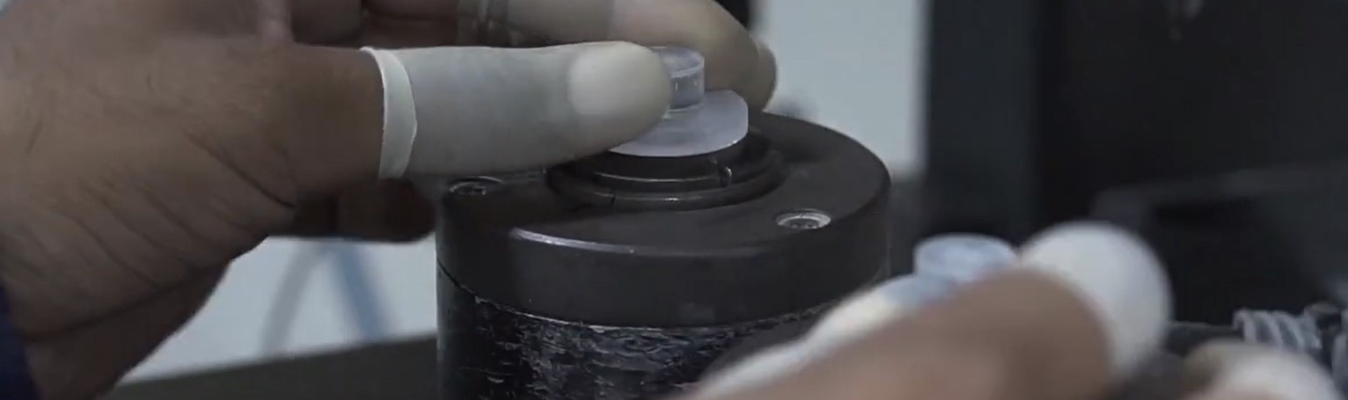
|
IPCL is a development of the Care Group. Headquartered in Vadodara, it was founded in 1987 and today employs over 2,000 people. |
Care Group began manufacturing IOLs in 1991 and is now one of the largest IOL manufacturers in the world. As an innovative company, it has registered 14 patents in four years making it a world leader.
The idea and development of the IPCL began in 2010. The aim was to create the most advanced phakic posterior chamber lens that offers better solutions to the challenges posed by this type of refractive surgery.
In the development of the IPCL, Care Group designed a special material that meets the requirements for this type of lens. They aimed to create mechanical stability at very low material thickness, biocompatibility, with the best optical properties.
The second focus of the development was on the design to achieve an atraumatic, complication-free, and long-term stable fit.
Manufacturing commenced in 2014 and after four years of research, IPCL V1 was launched. It was followed in 2017 by the second generation (V2), which brought further improvements in the design.
IPCL manufacturing process
IPCL manufacturing starts with the specific material blanks, that Care Group produces itself. The production of a blank takes two weeks.
IPCLs are manufactured on special lathes for ophthalmic applications by Sterling Ultra Precision, the leading manufacturer in this field.
Six blanks go into manufacturing per order, i.e. per eye. Ultra-precision diamond lathes are first used to lathe the geometry, sphere, torus if applicable and, the diffractive rings of the optic from the blank. Next, the openings are drilled and the contour of the IPCL is cut out of the block.
For IOLs, machines with precision in the micrometre range are commonly used worldwide. Care Group uses machines with precision in the nanometre range for IPCL. Also, the diamonds of the heads, which are usually “good” for up to 10,000 cuts, are replaced every 2,000 cuts in IPCL production.
Once the “raw” IPCLs are made, they are polished with an ultra-fine granulate for about 15 hours to achieve a perfect surface and round edges.
This is followed by the hydrogenation of the lenses before the crucial steps:
- 100% quality control – every single IPCL is checked without exception.
- Parameters: – the shape and surface are checked for defects. This includes base refractive value, MTF, if applicable torus with axial position, all focal points of Presbyopic IPCL and of course the size is measured. Only when all parameters are in the narrow “green zone” is the IPCL packed, labelled, and sterilised.
Initially six blanks are sent on the 14-day journey through production to ensure that at least two pieces pass strict quality control. Usually however, it is four to six that receive the “IPCL by Care Group” seal.
Experienced workforce
High quality is not only achieved by the precision of the machines and processes, but also by the experience of the employees. Those involved in IPCL manufacturing have developed skills over many years in-house IOL production. In addition, the IPCL is only produced on a day shift. Quality control is entrusted to 20 hand-picked employees who have at least 15 years of experience in IOL quality control.
It is only through individual production to order that it is possible to offer the almost unbelievable range of IPCL variants. For the monofocal aspheric IPCL there are “only” 1,183 variants. The monofocal toric has 809,172 options and the presbyopic-toric has 2,569,320. In total, there are “just” 3,384,433 IPCL variants in the standard range! Everything, from the material to the finished lens, comes from a single source.
This breadth and depth of IPCL production is unique – at least for an IOL.